Terrazzo Finishes
- bradhedges
- Jan 25, 2021
- 5 min read
Updated: Aug 25, 2021
In this post we are going to discuss finishing terrazzo. There are two main options to finish terrazzo:

1. Standard Topical Sealer
2. Premium High Polish System
We’ll start with the topical sealer as that is the industry’s standard. The NTMA specifications call for epoxy terrazzo to be ground and polished to a minimum of 120 grit and sealed with a generic topical sealer.

It is important to ensure that the terrazzo control samples and the terrazzo specification are consistent with each other. Please consult with your terrazzo manufacturer to obtain this information. For example, if your samples are sealed with a Specific Water Based Urethane Sealer, such as Terroxy WB Urethane. The terrazzo specification should also reference that. Further, when reviewing Submitals, designers should confirm the sealer is the same to ensure the specified performance.

Sealers offer varying performance and should be selected based off the variables of each buildings environment and owners maintenance preferences. The sealer is a sacrificial wear layer and stain protection for the flooring.

There are two basic categories for the sealer types:
1. Acrylic
2. Urethane
Generally Acrylic sealers are more affordable, don’t last as long and are easily removed using a seal stripper. Thus, they lend themselves toward the strip and recoat process. Generally you can expect to get around 1 year of wear out of an acrylic sealer.

Generally Urethane Sealers are slightly more expensive, last longer and have better chemical resistance. However, when it’s time to remove them, it’s a slower removal process as they are mechanically removed. Generally you can expect between 1-3 years from a Urethane sealer.

Both types of sealers are offered in both Water Base and Solvent Base. In today’s construction, Water Based Sealers dominate the market due to Indoor Air Quality standards and concerns. Solvent Based Sealers contain harsher chemicals that typically don’t permit them to be used indoors, however, they may still be used in exterior applications. There are many different types of sealers. The main difference between them is the solids content. This is the actual amount of product that remains after the sealer has been applied. For example, if you have a sealer with 27% solids, the remaining 73% evaporators during application. The higher solids content the more durable the sealer will be. This is good to check when reviewing the submittal product data.
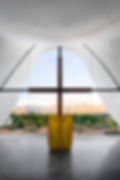
Sealers also offer different sheens so it’s important to understand the look they produce. You can specify, Matt, Satin, Semi Gloss or Gloss finishes so be sure to communicate this to your terrazzo manufacturer to ensure you get the correct finish. Again, I want to remind designers to carefully review the product data of the contractor submittals to ensure they are consistent with the approved control sample and specification. Spec sections 2.03 Sealer and sections 3.03 and 3.05 should all be consistent. I also encourage designers to work with the terrazzo contractor to have a larger mock up. This will show the finish much better than the smaller samples. The mock up should then be used as the standard of quality.

Sealers are also directly related to the slip resistance of the terrazzo flooring. When you have a sealer the building occupants are actually walking on the sealer rather than the surface of the terrazzo. The terrazzo industry uses ASTM D-2047 for testing the coefficient of friction.
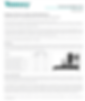
To protect the owner from slip and fall liability, designers want to ensure the test results are .6 or above for typical walking surfaces. If there are sloped or ramped surfaces designers want to ensure the test results are .8 or higher. This test is run both wet and dry so check both readings.

As of recently ANSI/NFSI B101.3-2012 Test Method for Measuring Wet DCOF (Dynamic Coefficient of Friction) of Common Hard-Surface Floor Materials has become a more common testing requirement. Using this test designers want to ensure test result are .42 of greater in order to be certified high traction. TRx Coating is compliant with this testing and achieves .42 or higher.

Terrazzo is a ground and polished surface and is often perceived to be a slippery surface, however, with the right sealer terrazzo can be compliant with both of the above mentioned tests.

Occasionally I have clients ask if there is anything else that they can do the further increase the slip resistance of the terrazzo flooring. Slip additives such as abrasives can be mixed or broadcast into the sealer to create a texture that offers more slip resistance. While increasing slip resistance I always like to remind designers that the textured surface will attract dirt and will require more care. Below are some examples. My preference is the micro glass bead from Terrazzo & Marble Supply as it creates a nice texture that is not to aggressive so it’s easier to maintain.

Some sealers are softer than others and thus can be more prone to scuffing. This can be particularly problematic for light colored floors. Using a harder sealer or burnishing will help with the scuffing issue.
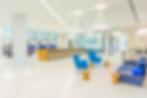
Sealers can also affect the color saturation of the terrazzo. Particularly TRX Coating. This is a high performance product that brings out rich color saturation and also offers excellent durability and chemical resistance. It’s my preferred sealer for particularly demanding environments such as bathrooms, labs or hospitals. TRX Coating is also a hard sealer so it has good scuff resistance. Just like most things in this world you get what you pay for. The terrazzo sealer is the least expensive component of the terrazzo flooring but has a major impact on the final aesthetic of the floor. It can really make or break the finished look of your project.

If you have a sealed terrazzo floor you should follow these maintenance guidelines.
The alternative to the standard topical sealer is the high polish system. In this case the terrazzo contractor will continue to polish the terrazzo up through progressive grits to a minimum of 800 grit. Then apply the finishing compound such as with SentryHard and SentryGuard or 3m stone protector. The main benefit of this is building occupants walk on the actual surface of terrazzo.

This provides a harder surface, more natural appearance and increased reflectivity. Depending on building traffic the finish typically will last 3-5 years. This finish does cost more (around $3 per sf) as the terrazzo contractor must do a minimum of three more passes over the floor so you are paying for more labor. There are many variables with a high polish system which can affect the slip resistance. Please check with your finish supplier to ensure proper slip resistance is achieved with their system.

As of recently, we've had some owners such as RDU do a high polish but not apply a finishing compound or impregnating sealer. I really like this concept and believe it is one of the best ways to finish an epoxy terrazzo floor. However, we need to keep a few things in mind. While the epoxy resin is impervious the remaining 70% of the floors surface area is the aggregate mix. The aggregate mixes vary but usually contain some percentage of natural stone, typically marble. Marble has a low porosity so it has the potential to stain. This is typically not an issue for most aggregate colors. However we should be careful when you have a white on white floor with white marble aggregate. If you had a spill it could stain the light colored marble chip.
Once you have approved your terrazzo colors, I encourage you to consider the terrazzo finish and make sure you have properly specified the correct finish and obtained a sample.
The last thing I’ll address is proper protection. Regardless of the finish selected a commercial job site is a tough environment so be sure to properly protect the terrazzo floor with ram board or similar.
I hope this has been helpful. Please let me know if you have any questions. Thanks!